Plastic Material for Bottles
Factors such as strength, durability, aesthetics, and cost must be considered when selecting the appropriate plastic for each application. By carefully considering the properties of plastics and the manufacturing processes used, we can create products that are stronger, more durable, and more aesthetically appealing for your brand.
We know it as PETE or PET plastic. Most frequently used in water and beverages bottles, food jars and containers, salad dressing and oil bottles, clothes fiber, mouthwash bottles. Plastic #1 is usually clear in color and it is not intended for multiple uses. Contact us with your requirements!
Recognized as one of the most versatile polymer materials, HDPE has some benefits that make it a popular choice for plastic bottles. HDPE is considered safe and has a high molecular weight. This kind of plastic can be recycled repeatedly without losing strength or quality.
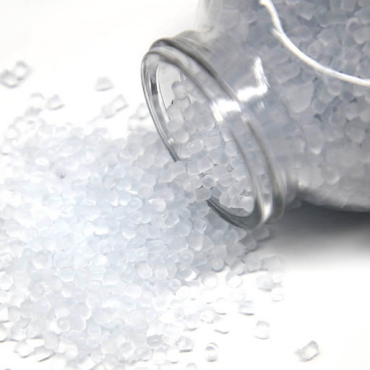
Bottles made from PVC are durable bottles ideal for shampoos, oils, and other products that require long term storage. New PVC plastics work well for hot fill applications and can withstand temperatures up to 140° F. PVC bottles retain a streaky finish when clear. Message us now!
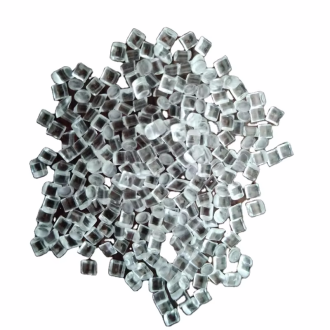
LDPE is used in the production of a wide range of containers, squeeze and dispensing bottles, tubing, computer parts, lab equipment, and numerous caps and closures. It is nearly unbreakable because of its strength. It’s most common use is in plastic bags for food shopping.
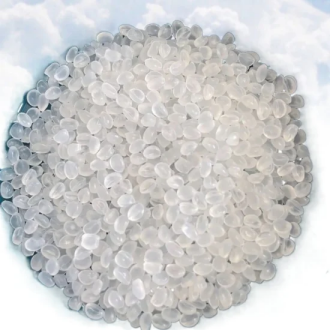
PP is the material most baby bottles are made from. It is a lightweight and durable plastic that is safe for use with baby bottles. They are affordable and widely available in the market and also BPA-free, making it a safer option for your baby’s health. PP is molder-friendly, translucent and easily colored. Contact us!
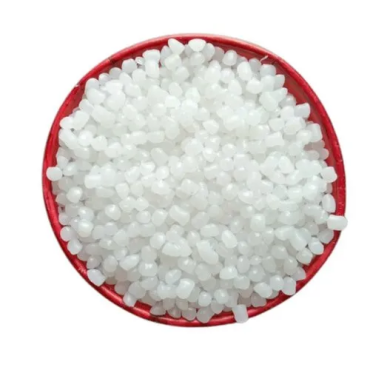
Polystyrene is known for its clear appearance and rigidity, making the bottles great for applications where product visibility is a must. PS can be cast into molds with fine details such as graduated measurements allowing it to be suitable for laboratory bottles like test tubes and some cosmetics and medical applications.
Plastic Film Selection
As entrepreneurs, you are aware of how crucial it is to spend money on premium packaging in order to protect goods while they are being transported and stored. In the food and beverage, agricultural, medicinal, and healthcare sectors, bags and pouches are extensively utilized for product packaging. Here at Shenzhen Shengheng, we offer custom manufacturing and printing of packaging bags of all shapes and sizes, making it easy for you to both attract customer attention and comply with labeling regulations.
Printing Technology
Using the correct printing method for packaging is significant, your best option will be dependent on several unique aspects. Depending on the type, size, shape, and design of the package, having a better knowledge of the variants to make the best option for unique needs is very important. Let’s see the different printing methods available:
Kraft Paper/PLA Compostable Materials
Kraft Paper/PLA foil laminate is intended to achieve fully compostable materials in a eco-friendly way. PLA film functions as an inner sealing layer. However, because PLA film and kraft paper are not barrier films, the final foil lamination cannot be intended for use as a barrier package. As a result, the quality and smell of the coffee cannot be guaranteed when the coffee beans, for example, are packaged in this compostable bag.
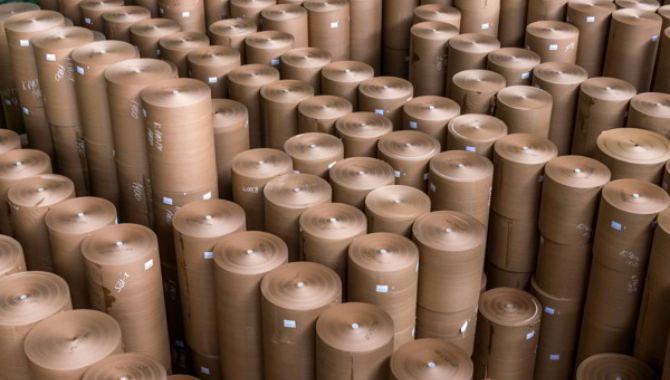
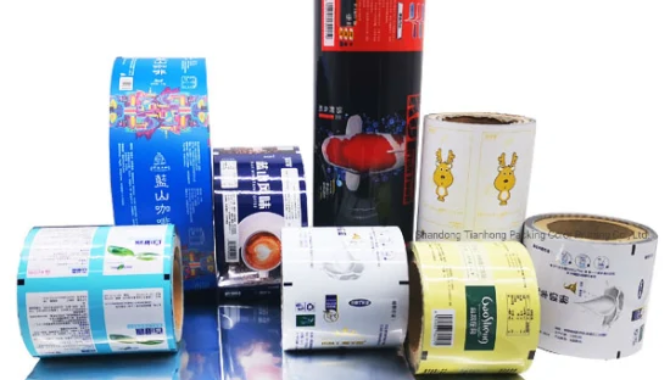
Kraft Paper/VMPET/LDPE Foil Film
This combination is taken as the most used packaging film materials for kraft paper coffee pouches or coffee packaging bags.
BOPP/VMPET/PE Film
The most popular product pouch packaging choice, the pillow bag is used in many industry types. One combination for snack bag is food grade BOPP/VMPET/PE. Pillow pouch typically contains a bottom and top seal, with a back seal that helps form the “pillow” shape. Pillow pouches can be made using one material only or range from multi-layer plastic films.
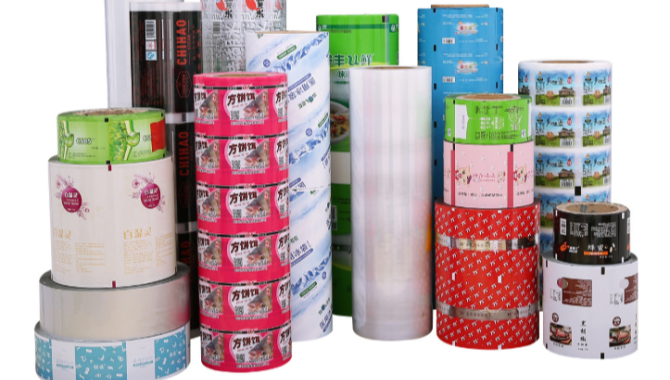
“Cost Efficiency on Choosing the Right Materials”
Choosing the appropriate packaging materials can affect costs at every stage of a product’s life cycle, from disposal to manufacturing and shipping. Reducing production costs, streamlining logistics, and lessening environmental impact can all be achieved with the use of lightweight, easily obtainable materials. Furthermore, minimizing the chance of damage or loss can lower the cost of returns or replacements by selecting strong materials that adequately safeguard products.
Plastic packaging is popular due to its versatility, durability, lightweight nature, and cost-effectiveness. It fits many businesses and provides a multitude of choices for packing different kinds of goods.
Many plastic packaging materials are recyclable, but the recyclability depends on the type of plastic used and local recycling capabilities. It’s essential to check with local recycling programs for specific guidelines on recycling plastic packaging.
Yes, there are alternatives to traditional plastic packaging, including biodegradable plastics, compostable plastics, paper-based packaging, and reusable packaging solutions.
Plastic packaging is often competitive with other packaging materials in terms of cost, offering several advantages that contribute to its affordability like low production costs, lightweight nature, durability, customization and reusability.
Yes, plastic packaging is often durable enough to protect products during shipping. Plastic packaging materials such as PE, PP, and PET offer excellent durability and resistance to impact, moisture, and environmental factors.